Bone and heart from the 3D printer: we visited the Laboratory of the University of Pécs
Did you know that 3D printing technology can now be used to produce artificial limbs or arms? And that advances in technology have made it possible to print "bones" that have the same properties as human bone, making surgery safer? We visited the PTE 3D Printing and Visualization Centre at the University of Pécs (PTE) where we saw such wonders. If you're interested in these scientific achievements, you could visit them in Budapest on the Night of Museums.
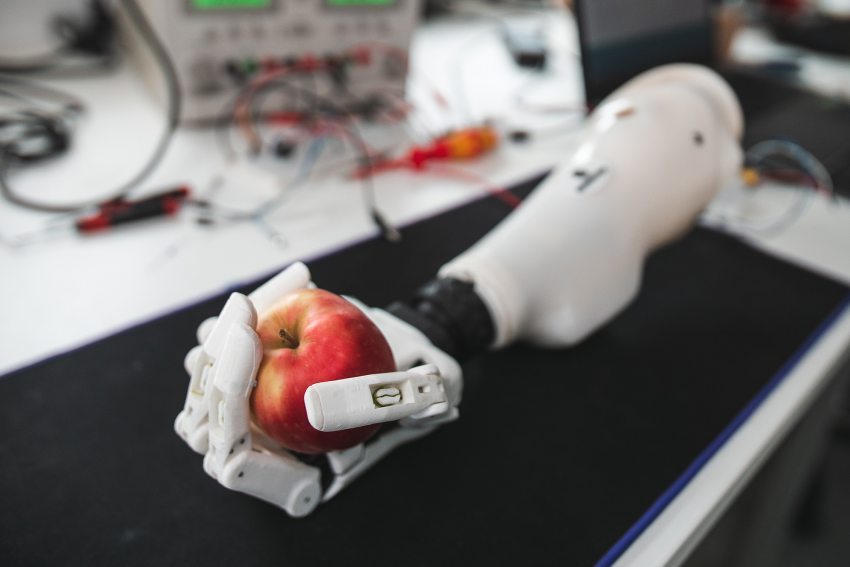
"A few years ago, Miklós Nyitrai, who is now the dean of the university's medical faculty, supported a tender, which allowed us to start planning the 3D project with the funds we received", says Attila Péntek, the professional coordinator of the PTE 3D Printing and Visualisation Centre, after my arrival, showing me around the Pécs laboratory. He adds that it was then that they decided which printers to buy, which topics to focus on, where to place the equipment they had purchased through the tender and started looking for competent staff.
Back then, the biggest problem was the latter: finding people who understood the technology or at least wanted to learn it.
Initially, they were given a room in the biophysics faculty but soon moved to a new building. They started with ten simple printers, based on so-called FFF technology, which were used to print a very rudimentary version of medical prostheses. Sometimes a device was printed for more than fifty hours. (The simpler, cheaper machines, based on the FFF technology mentioned above, costing between 300 and 400,000 HUF, are still in use on the upper floor of the laboratory, where they were printing continuously when we visited. The SLA printers cost more than that, between 2 and 3 million HUF, but - in general - still serve the average user and companies engaged in small series production.)
During this period, they explored the potential of machines with medical and engineering students. With their involvement, they began to build and test various simulators. They began to understand what materials had to be put into what form to make a sellable, usable simulator that was a little more capable than its competitors on the market. This was helped by the medical students' continuous testing of the prototypes.
For example, the various bones that help students to get hands-on training. They make a 3D printed model and then pour silicone around it to make a mould for mass production. The outer, hard part of the "bone" is then made first, and then the softer "marrow" material is poured into the silicone mould.
Many hours of work are spent on experiments, Attila explains, sawing, drilling, screwing, and continuous (medical) feedback to make the bone material resemble the real human bone as much as possible, as this is the best way to help education.
Help for surgeries
In addition to training medical students, they also print "practice bones" for certain surgical procedures. The resulting CT scan is scanned and the bone is printed. This helps the doctor to "practice" before surgery, rehearsing where and how to perform the procedure.
This option can shorten the operation time and reduce the risk because the doctor can be more confident about the procedure.
We spend a long time in this room, where they also make elbows with "skin", "flesh", and "nerves", and they also print hearts, which can even imitate the heartbeat and breathing.
Then we stop by a pile of "bleeding skin", one of the lab's most successful simulators. It bears a strong resemblance to human skin: a cross-section of the human body with different layers, and a small container hiding under the "skin" containing "blood" so that medical students can practice surgical laryngectomy on it.
A lot of experimentation went into making the surface of the device most like the feel of skin. They use a mixture of silicone and foam to try to recreate human skin in a way that doctors believe is most similar to the real thing. This recipe is a secret, completely unique development. It also required a lot of experimentation on how to glue the multiple layers together, how to place the blood pouch below the surface.
Meanwhile, we walk on to the moulding room where the demonstration instruments (bleeding skin, bones, organs) are made, one by one or in small series. János Mendler, who has decades of experience in modelling and injection moulding, is designing a model on his computer. Among other things, his experience has helped the PTE 3D Printing and Visualisation Centre to turn towards simulators that are competitive.
Hope for people with arms or legs
Attila Péntek picks up a prosthesis from one of the tables. This device is another success story of the lab. Inside it are two surface signal sensors that detect mechanical signals from two main muscle groups.
These muscle groups retain the ability to move the wrist and fingers even after amputation.
Thus, when the case, which is equipped with so-called myoelectric sensors that use electrical signals from the muscles, is attached to the remaining arm, the muscle groups can move the fingers of the 3D-printed prosthetic hand at the end of the case. (The prosthetic case is made by the medical device producing company Corvus-Med, with which the lab works in symbiosis.) Due to working principles, the case must of course be made separately for each patient.
Printing, designing and the production of a prototype are all done in the lab. Many versions of the prostheses have been developed, many of them just to see how the different parts and mechanics behave in real life, and then to see how and on what path to take for further work. In the second round of investment, which will be launched in the near future, the Centre expects to be able to attract further funding to make further improvements.
In addition to printing and education, research is also carried out in the lab. They can print teeth, braces and even the pliers used to pull them. The latter device has been tested with dentists, some of which had to be reinforced with glass fibre to make it more usable.
The university also generates income from the many products. For example, the bleeding skins are sold to research centres in hospitals. In addition to medical developments, there are also ongoing orders from industry, such as the automotive industry.
The future lives here with us
On the lower level of the building, there's more excitement, with huge printers serving industrial needs. The Stratasys J750 polyjet printer is priced at well over 100 million HUF, but it can now print in colour. The principle of operation is similar to that of conventional printers, except that in 3D, in the ink cartridges plastic (photopolymer) is used instead of ink powder.
The machine builds up the print layer by layer, and where a small part of the model protrudes, it prints a support from the tray level, which can be removed from the model later. We can imagine the function of the support material as the support pillar in a house under construction, which supports the vault.
The machine sucks the materials into the print head under vacuum, then the head mixes and drops the coloured plastic onto the tray. The top of the drop is cut off by a blade to allow the next drop to fit precisely. Finally, the machine firms the print with UV light. At the end of printing, the support material is washed off with water.
A smaller brother of the printer is ideal for dental printing. Based on a CT scan, the model is segmented and the denture is printed.
Its use helps when making braces, as the dental technician can rehearse the most ideal position and prefabricate the restoration, which can then be fitted into the patient's mouth. A silicone gum is also created to the printed denture in the lab, shows Attila Péntek.
In the lab you will find a room that looks more like a space base. Here you will find a printer that prints from polyamide in an insulated chamber. The inside of the chamber is heated to a temperature of 160 degrees Celsius, and then a laser is used to melt the injected material, which is more porous than flour. This process forms the object to be printed, with the printer also moving from layer to layer. At the end of the process, a large block of dust is created, from which, like Indiana Jones in the desert, the print must be carefully extracted by the technicians.